Groschopp Publikationen & Presse
Groschopp entwickelt umweltschonenden Elektromotor für Multifunktionsfahrzeuge
Muffel+: Hybrides Mobilitätskonzept für Multifunktionsfahrzeuge
Die Groschopp AG produziert seit mehr als 70 Jahren kundenspezifische elektrische Antriebe für verschiedene industrielle Applikationen. Dabei legt das Unternehmen aus Viersen großen Wert auf eine nachhaltige und qualitativ hochwertige Produktion umweltschonender Antriebstechnologien.
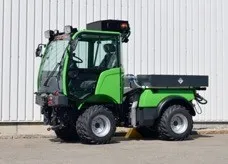
Im Rahmen des Verbundprojekts Muffel+ hat der Hersteller eine kompakte, skalierbare elektrische Antriebsplattform für verbrennungsmotorbetriebene Multifunktionsfahrzeuge entwickelt, die es ermöglicht, in diesem Bereich flexibel, energieeffizient und schadstoffarm zu agieren.
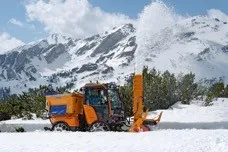
Nutzfahrzeuge mit Verbrennungsmotoren verursachen vor allem im städtischen Bereich erhebliche Lärm- und Schadstoffemissionen. Eine Lösung, um dem entgegenzuwirken, liegt in der Elektromobilität. „Genau hier sehen wir die Chance, einen zukünftigen Wachstumsmarkt durch frühzeitige Investitionen in Forschung und Entwicklung zu erschließen“, berichtet Alexander Klupp, Leiter Konstruktion bei Groschopp.
Aus diesem Grund hat sich das mittelständische Unternehmen dazu entschieden, sich an der Entwicklung einer skalierbaren elektrischen Antriebseinheit für Multifunktionsfahrzeuge zu beteiligen. Im Rahmen eines Entwicklungskonsortiums erstellte der Antriebsexperte zusammen mit der Hochschule Düsseldorf den Elektromotor für Muffel+. An dem Gesamtprojekt, das den Komplettantrieb inkl. Motor, Getriebe und Steuerung umfasst, waren federführend die Max Holder GmbH, sowie weitere Projektpartner wie die REFU Drive GmbH, die Nantis GmbH, die Hochschule Aalen und die Universität Stuttgart beteiligt.
Eingebettet ist das Vorhaben in das von der EurA AG geleitete Innovationsnetzwerk e-mobility, das die deutsche mittelständische Industrie für die zukünftigen Herausforderungen der Elektromobilität fit machen soll. Das Projekt wird im Rahmen der Maßnahme KMU-NetC vom Bundesministerium für Bildung und Forschung mit rund 2,1 Millionen Euro gefördert.
Smart, kompakt und energieeffizient: Muffel+
Muffel+ steht für die Erforschung, Entwicklung und vor allem funktionssichere technische Realisierung einer kompakten, elektrifizierbaren Antriebsplattform für Multifunktionsfahrzeuge – wie z. B. selbstfahrende Arbeitsmaschinen im Landwirtschaftsbereich oder allradgetriebene Kommunalfahrzeuge. Neben dem Fahrantrieb müssen in Anwendungen dieser Art meist auch Nebenaggregate wie z. B. Bürsten, Schneefräsen oder Häcksler angetrieben werden. Durch ihre Skalierbarkeit kann die Antriebsplattform flexibel auf die jeweilige Anwendung zugeschnitten werden. Vordergründig sollen die Fahrzeuge rein elektrisch arbeiten, bei besonderer Beanspruchung oder zum Speisen der Batterie kann jedoch auch ein Verbrennungsaggregat zugeschaltet werden. „Die Steuerung schaltet den Verbrenner bei Bedarf zu oder ab, so dass der Motor permanent mit optimalem Wirkungsgrad betrieben wird“, erklärt Klupp. „Zukünftig soll auch ein rein elektrischer Betrieb mit Brennstoffzellen möglich sein.“
Effizient und kostengünstig
Die Max Holder GmbH stellt für das Gemeinschaftsprojekt Karosserie und Fahrwerk für Funktionsdemonstratoren eines elektrisch betriebenen Multifunktionsfahrzeugs zur Verfügung. Neben den realen wurde auch ein virtueller Funktionsträger für Simulationen und Analysen erstellt. Die Nutzung von Demonstratoren ist für alle Projektpartner wichtig, um verschiedene Einsatzszenarien zu erproben und Bauteile sowie Komponenten entsprechend anzufertigen, zu testen und zu optimieren. Die Leistungsfähigkeit des Antriebs wurde zum einem auf verschiedenen Prüfständen, zum anderen im Feldversuch auf der Teststrecke von Max Holder erprobt.
Um den Anforderungen eines möglichst energieeffizienten und schadstofffreien Antriebskonzepts gerecht zu werden, wurden verschiedene Motoren hinsichtlich ihres Wirkungsgrads, ihrer Drehmomentdichte, Überlastfähigkeit, Regelbarkeit und Produktionskosten bewertet. Die Synchronreluktanzmaschinen (SynRM) und permanentmagnetunterstützte Synchronreluktanzmaschinen (PMaSynRM) mit Ferritmagneten von Groschopp schnitten dabei am besten ab. Durch ihren hohen Wirkungsgrad sind sie in der Lage, Verluste zu reduzieren und die Reichweite des Fahrzeugs zu maximieren. Die Verwendung einer kleinen Batterie senkt die Investitionskosten und trägt dem knappen Bauraum Rechnung. Der Verzicht auf teure Seltenerdenmagnete unterstützt die wirtschaftliche Herstellung des Motors.
Anforderungen an den Elektromotor
Die Elektromotoren sollten zusammen mit den Getrieben als Antriebseinheit in den Achsmodulen verbaut werden. Ein Achsmodul wurde zuerst als virtueller Funktionsträger erstellt, an dem die wesentlichen Eigenschaften validiert und Funktionalitäten überprüft wurden. Ein physischer Aufbau erfolgte dann in enger Abstimmung mit Max Holder. Aus dem Fahrzeugkonzept wurden die Anforderung an den Elektromotor abgeleitet: Neben den mechanischen Schnittstellen zum Achsmodul, dem Getriebe, den Anschlüssen für das Kühlwasser, der Stromversorgung und Sensorik sowie den Störkonturen betraf das auch die Arbeitspunkte verschiedener Anwendungen sowie die zur Verfügung stehende Kühlwassertemperatur.
Die Entwicklung des Elektromotors erfolgte in enger Zusammenarbeit mit der Hochschule Düsseldorf. Der Schwerpunkt der Universität lag auf der Auslegung des elektromagnetischen Kreises, der Dimensionierung des Motors und der Festlegung des Funktionsprinzips. Groschopp war für die Umsetzung des Konzeptes insgesamt verantwortlich. Dies betrifft insbesondere den mechanischen Aufbau, die zu berücksichtigen Anforderungen des Lastkollektivs sowie die Entwicklung eines geeigneten Kühlkonzepts für den begrenzten Bauraum im Fahrzeug.
Aufbau des Elektromotors
Schlussendlich wurde der Motor in einem speziell geformten, doppelwandigen Aluminiumdruckguss-Gehäuse untergebracht. Dennoch musste das Fahrzeug angehoben werden. Die hohe Leistungsdichte und Verlustleistung erforderten zudem eine Wasserkühlung. Ein wesentlicher Entwicklungsschritt stellte die Erforschung und Entwicklung der Rotorstruktur dar. Die Störkonturen erforderten einen nach innen geformten Wickelkopf auf der B-Seite des Ständers – hohe Temperaturen Isolierstoffe bis Klasse N (200°C). Und um Kosten zu sparen, wurde ein kommerzieller 4-poliger Blechschnitt mit einem Außendurchmesser von 200 mm und einer Länge von 110 mm verwendet. Bei der Auslegung des Blechschnitts für den Läufer musste ein Kompromiss zwischen den Anforderungen eines optimalen elektromagnetischen Kreises, der mechanischen Festigkeit und der Kosten gefunden werden. Mit in die Flusssperren eingebrachten Permanentmagneten konnten höhere Drehmomente und Drehzahlen erreicht werden. Die eingebrachten Ferritmagnete reduzieren zudem die Verluste des Motors um bis zu 30 Prozent.
Ein erfolgreicher Abschluss
Groschopp ist es im Rahmen des Projekts Muffel+ gelungen, das theoretisch Machbare mit dem wirtschaftlich Sinnvollen zu kombinieren und eine Lösung zu finden, die kostengünstig und dennoch solide ist. Die fertiggestellten Demonstratoren wurden an Max Holder, Refu Elektronik sowie an das Institut für Leistungselektronik und elektrische Antriebe (ILEA) der Universität Stuttgart sowie die Hochschule Aalen für weitere Prüfstandtests übergeben. Diese dienten zur Durchführung weiterer Versuche zur Optimierung verschiedener Komponenten – wie der Frequenzumrichter, Getriebe, sowie des Kühlkreislaufes. Aufgrund der hohen Anzahl der zu fertigenden Demonstratoren und der aufwändigen Einzelfertigung der Gehäuse hat sich Groschopp zur Beschaffung von Druckgussformen entschieden. Damit konnte der Hersteller bereits Erkenntnisse für eine zukünftige Serienfertigung gewinnen. „Insgesamt zeigten die Tests eine gute Übereinstimmung zwischen den vorberechneten Motordaten und den real durchgeführten Messungen“, so Klupp. „Daher liegen die daraus folgenden Optimierungsschritte nahe am jetzigen Stand der Technik, was sich positiv auf die Fertigung und insbesondere die Lieferzeit der nächsten Prototypen auswirkt.“
Insgesamt erforderte Muffel+ das Wissen und die Erfahrungen aller Beteiligten von der Erstellung des Lastenheftes bis hin zum Entwurf eines Gesamtkonzepts sowie der anschließenden Fertigung der Komponenten und Prüfung. Dank der guten Zusammenarbeit aller Projektpartner konnte das Vorhaben erfolgreich umgesetzt und im Sommer 2020 zum Abschluss gebracht werden. Inzwischen wurde der Funktionsdemonstrator komplett aufgebaut und das Gesamtsystem absolviert derzeit umfangreiche Systemtests für den Einsatz in unterschiedlichen Applikationen. „In Zusammenarbeit mit den Projektpartnern und auch weiteren Unternehmen bzw. Institutionen streben wir eine Weiterentwicklung des Antriebs für Anwendungsfelder wie Baumaschinen, Landmaschinen und Flughafenfahrzeuge an“, so Klupp abschließend.
Infokasten
Arbeitspunkt | Drehzahl | Drehmoment |
Straßenfahrt | 8.626 1/min | 6,27 Nm |
Transportfahrt | 3.882 1/min | 21,51 Nm |
Winterdienst | 864 1/min | 37,47 Nm |
Kehren | 1.728 1/min | 15,23 Nm |
Hang (Acker) | 324 1/min | 65 Nm |
Weinbau | ||
(Acker) | 1.080 1/min | 65 Nm |