Groschopp News & Press
A clever processing module with a minutely adjustable feed rate
Individually and minutely adjustable feed rate is essential for dry-processing of drilling wood, aluminium, or plastics, to meet the demands posed by the textures of various materials and to avoid causing any damage. Servomotors made by Groschopp are incorporated in the linear-feed-axle of a clever processing module made by the company ToolDrives as an integral drive element, specifically modified for this particular application.
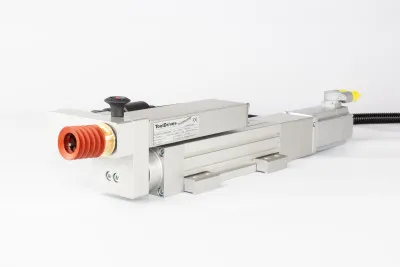
Every accomplished DIY-worker knows this problem: the wall to be drilled is sometimes too hard, while at other times it is relatively soft, or even has an in-between texture. Accordingly, the DIY-worker has to use the power drill adeptly and with an appropriate feed to obtain a hole cleanly drilled and without any broken edges.“Our newly developed processing module has an in-built intelligent system recognising such different material hardness”, explains Volker Meier, CEO of the company ToolDrives GmbH & Co. KG.“We have named this clever tuning combination between tooling, material, spindle speed and feed the ‘DNA’ for drilling perfect holes.”

The company ToolDrives was founded only recently in 2019 and is situated in Medebach, North-Rhine Westphalia. The company specialises in developing, manufacturing and marketing direct tool drives for CNC-heavy-duty dry processes. The portfolio of the company ToolDrives encompasses a turnkey system model kit, comprising a control box, including a suitable output- and regulatory electronics in a decentralised switchboard unit, as well as the appropriate software. It also contains an individual frame for attaching the processing modules at the machine console. The modules offer direct-driven spindles that can be designed on request variably and customer-tailored. ToolDrives has introduced a processing module to the market comprising intelligent software: it is the IHS-ADU60(Intelligent High Speed – Automatic Drilling Unit).
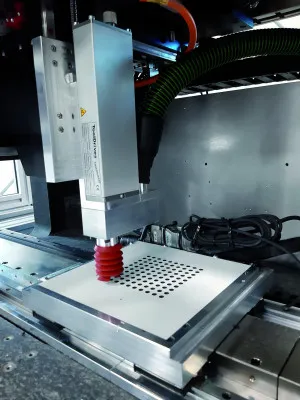
The way to drill a perfect hole
Specific to wood and timber processing, it is of utmost necessity to ensure that the material does not get damaged during a drilling process because scorch marks may be created due to the drill speed being chosen too high, or dwell time of the drill in the wooden material being too long. Moreover, the detection of foreign bodies is of utmost importance, e.g. a nail or other hard contaminants in the wood/timber should trigger an immediate withdrawal of the drill.
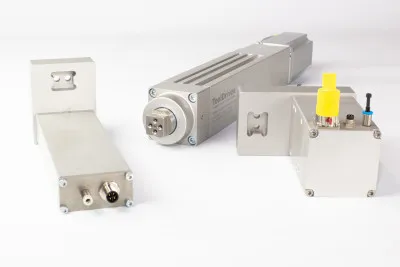
Such a sensitive feeling and the reaction to it – as if done by a human hand – is performed by the sensor system in combination with an intelligent controller in the new processing module. In that way, a minutely adjustable feed rate, respectively speed adjustment of the Groschopp servomotor, is made possible. The servomotor propels the linear axis for the movement of the tool. “When, for instance, a hole has to be drilled in a kitchen counter, the drill needs to move with a different feed and speed through the hard top layer than is needed in the remaining softer material”, Volker Meiercomments.
The system model kit of the IHS-ADU60 has a further advantage in that ToolDrives’portfolio comprises a suitable exhaust suction device for dry-processing operations. This exhaust suction, situated at the spindle, serves to prevent any lodging of fine dust and particles around the drilled hole and any remaining chips are safely removed.“Lots of components are painted or varnished after the drilling process, and that is why cleaning of components is so much easier”, Meier adds. Moreover, machines and the environment remain much cleaner. “Customers are enabled to drill perfect holes in a short time due to the symbiosis of all system components.”Areas of application can be found not only in the manufacturing of windows, staircases, and furniture but also in the bicycle- and automobile-industry using materials like wood, carbon, aluminium or plastics.
Connectivity and handling made easy
“We wanted to ensure a homogenous match between drive unit, sensor system and integrated output- and controller-electronics for our newest module IHS-ADU60”, says Meier. “We have cooperated closely with providers of electronics and with a manufacturer of servo-controllers in the past, who for many years had worked closely with the company Groschopp. Hence, we knew that the combination of motor and electronics have worked superbly well in the past.” The advantage is that parameterisation is unnecessary because the motor is automatically calibrated by the controller, and so the controller can detect which motor data and characteristics are available already at the initialisation stage.
The centralised core-element, respectively the so-called ‘DNA’ of the processing module, is the integrated LCM-electronics (Life Cycle Management) in the form of a micro-processor-board. It activates the pneumatic valves, processes sensor signals, and stores data, e.g. fault history or operating hours. Besides, it provides information about the characteristics of the module in respect of the installed spindle motor, the sensor system, and the attached tool fitting. Additional transparency is provided using a ‘Condition-Monitoring-Software’ in recording and evaluation data like torque, speed, output and positioning detection and allows the monitoring of spindle status and tool breakage to guarantee a frictionless production including optimal maintenance intervals. Easy handling in particular, and the optimal connectivity of the high-power Groschopp-motors used in the feed unit of the module, all combine to achieve perfectly fitting system components. Also, capacity, compact design, and little weight are advantageous, especially when used in robotics.
Design-engineered optimisation on request
Installed in the processing modules made by ToolDrives are servomotors of type EGK 48-60 NR of the Black Panther series made by Groschopp. These motors are characterised not just by their relatively small size and power density but are also particularly dynamic, precise in positioning, and they can be flexibly configurated. It is possible to integrate a servo-controller with these motors so that the installation space needed can be kept at a minimum. The servomotors can be equipped with a variety of sensor systems, and they fit extremely well in the ToolDrives-modular concept. Moreover, the surface of the drive units can be painted with a special coating or can be supplied in stainless steel by which they can be installed in particularly demanding environments, e.g. in the foodstuffs- and packaging industry.
Groschopp offers customers individually tailored drive solutions on request which satisfy any request posed by the respective application, and to that end, the servomotors for ToolDrives were equipped with a convenient single connection cable with integrated sensor- and power-cable. “What this means is that, instead of separate connection cables, we decided to use a combination- respectively a Hybrid-plug which simplifies significantly the cable duct at the robot or the machine”, says Meier. Besides, the connecting cable was positioned towards the endshield on the drive side to obtain a good fit for the motor in the application. “Even the sampling inspection at the starting phase and the provision of CAD-data went smoothly”, explains Meier. “In that way, we were able to provide our customers with CAD-models at the earliest time as soon as the prototype of the intelligent drilling module was completed, so that we could check whether the system would fit in the particular equipment.“
EGK-servomotors are only used in IHS-ADU60-modules at present, but the partnership with Groschopphas proved to be such a positive experience that the CEO of ToolDrives sees potential for further joint projects and envisages an extension of their cooperation.
EGK 48-60 NR data:
- Output– 320Watts
- Speed – 3000 minˉ¹
- Voltage – 325Volt
- Torque– 1Nm